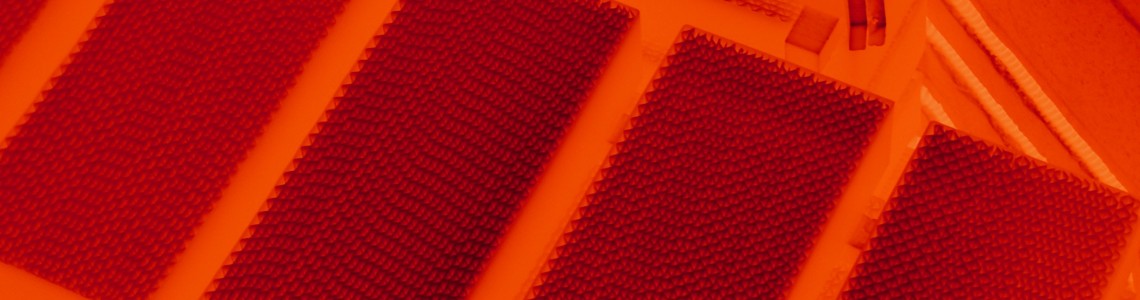
Above is a photo of Fireview Catalysts being oxidized at Woodstock Soapstone Company (April 2022) prior to being coated. The oxidation process creates an aluminum oxide (Al2O3) layer on the surface of the FeCrAl Ferritic Stainless Steel used to build Woodstock Soapstone Catalysts. The aluminum oxide layer is important to both the life and performance of the catalytic combustor, as explained below.
We make all the catalytic substrates (the metal part that the precious metal coating is applied to) for our wood stoves. Building the substrates in-house gives us greater control over both cost and quality.
The cells of our catalysts are composed of alternating layers of flat and corrugated stainless steel foil with high contents of Chromium and Aluminum, in combination with rare earth elements like Cerium, Hafnium, Lanthanum, and Yttrium. This alloy, CrAl6, was developed by MK Metallfolien a German company that also has plants in China, and the United States.
The high aluminum content in CrAl6, in combination with rare earth elements makes the foil suitable for applications up to 1200oC (2,192oF). These temperatures are generally unattainable in a woodstove, even with severe over-firing.
The oxidation process consists of heating the catalysts in batch mode, and then “soaking” them for a set duration in a specific temperature range. During the oxidation process, aluminum in the alloy diffuses to the surface of the foil during the high temperature “soak” and forms an aluminum oxide layer on the surface of the foil.
This
aluminum oxide layer is important for several reasons:
1. The aluminum oxide on the surface of the foil protects the metal substrate from oxidation that would otherwise occur to the metal substrate at the operating temperatures of the wood stove. It increases the longevity and durability of the catalyst.
2. The surface of the aluminum oxide layer has a microstructure that often looks like leaves or small plates. These surface structures increase the surface area per volume, and the increased surface area maximizes the number of reactions that can occur.
3. We use the aluminum oxide coating to bond the layers of the catalyst together to form a monolithic honeycomb structure. This is very important, because woodsmoke contains a number of chemical compounds that have adverse reactions with brazing materials. This is less important when fabricating catalysts for diesel or gas engines, where the composition of the exhaust is known, but for woodstoves bonding the layer of the catalyst together with any sort of brazing is an invitation to trouble.
4. The rare earth metals added to the alloy are known to improve adhesion of the aluminum oxide layer to the underlying foil, thus improving both longevity and high temperature performance.
The images to the right (sections and surface detail) are images of Woodstock Soapstone catalytic combustors taken with a Scanning Electron Microscope at the Dartmouth College graduate Department of Engineering.
We continue to investigate possible improvements in oxidation resistance and good aluminum oxide film adhesion because we think they are essential to good catalyst performance. The manufacture and oxidation of woodstove catalysts is a time-consuming and arduous arduous task, but we have arrived at a stage where our catalysts are virtually trouble free and perform up to our expectations.
Later this summer we plan to retrieve some catalysts from our customers to further examine how the aluminum oxide layer has weathered 3-4 years of use. We also expect to experiment further with our oxidation process. We expect to be able to report more news in the late summer or fall.